Expert Techniques for Metal Fabrication and Welding Services
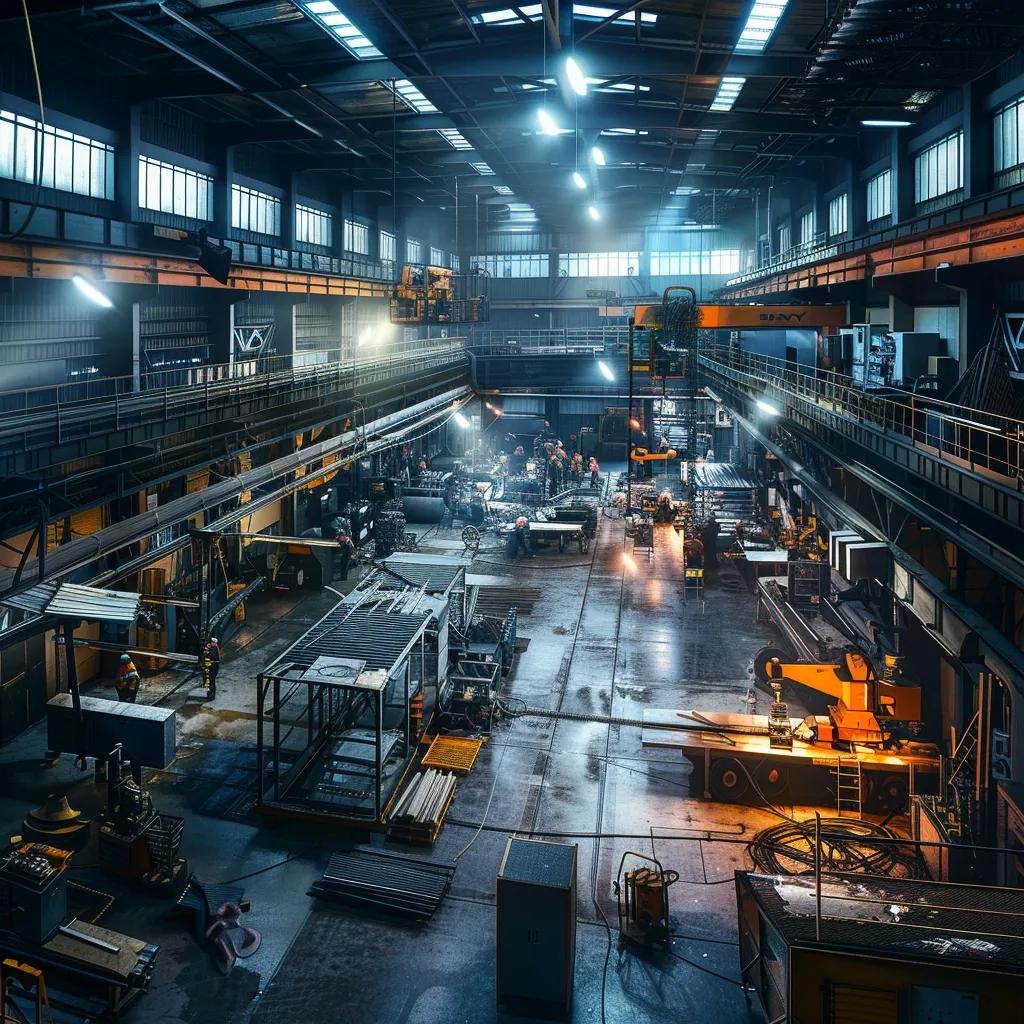
Custom Welding & Fabrication Services

In today’s highly competitive industrial landscape, custom welding and fabrication services have become essential for a broad spectrum of manufacturing and construction projects. Businesses ranging from large-scale production facilities to small specialty welding shops require expertise in aluminium welding, pipe work, metalworking, and the joining of diverse materials such as steel, stainless steel, and carbon steel. The increasing demand for precision welding techniques—from arc welding and metalinert gas (MIG) welding to specialized services like
and orbital welding—reflects the growing need for quality control, engineering precision, and innovative design. Companies rely on certified welding inspectors, AWS-certified welders, and nondestructive testing methods to ensure that every weld meets stringent safety and quality standards as outlined by the American Welding Society. Custom fabrication involves not only joining materials but also designing and constructing components that support structural steel infrastructures, sheet metal assemblies, and boiler or pressure vessel constructions. In addition, mobile welding services and rapid prototyping through plasma cutting or stud welding empower businesses to meet tight deadlines, lower production costs, and maintain competitiveness. With the integration of modern technologies, such as laser and robotic welding systems, fabrication capabilities are constantly evolving to match the pace of manufacturing innovations, thus reinforcing the importance of high-quality welding and metal fabrication solutions. This article delves into the differences between welding and fabrication, outlines the types of welding and fabrication services available, details the capabilities offered by custom welding service providers, and finally highlights how to get in touch with Astro Machine Works for industry-leading, custom welding solutions.
Transitioning from quality service fundamentals to an in-depth exploration of the technical differences, we now examine the core concepts that distinguish welding fromfabrication.
The Difference Between Welding vs. Fabrication
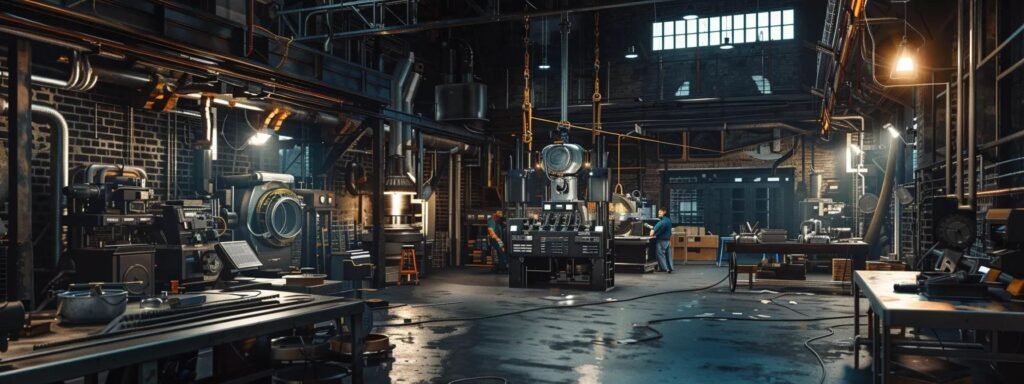
Welding and fabrication are integral processes in the metalworking industry; however, they each play distinct roles. Welding is the process of joining materials—typically metals—using high heat and specialized filler materials to produce a strong, permanent bond. Fabrication, on the other hand, encompasses a broader range of manufacturing activities, including cutting, bending, and assembling metal structures from various components. While welding represents one of the most critical steps in the fabrication process, fabrication itself includes design engineering, material selection, and post-weld treatments.
In a welding shop, the operator uses techniques such as shielded metal arc welding, gas metal arc welding (MIG), or gas tungsten arc welding (TIG) to ensure precise joining of parts. The quality control of these welds is often overseen by a certified welding inspector, who relies on nondestructive testing methods to verify weld integrity. In contrast, fabrication shops deal with a full spectrum of tasks—from creating prototypes using plasma cutting and laser welding services to scaling up production with custom welding and stud welding processes. Additionally, metal fabrication involves assembling various sections to form a unified structure, which can include the use of inert gas and shielding gas techniques to protect welds from atmospheric contamination.
Environmental factors such as heat, humidity, and the type of metal can dramatically impact both welding and fabrication processes. For example, aluminium welding presents its own set of challenges due to the metal’s high thermal conductivity and susceptibility to oxidation, requiring specialized knowledge and equipment. In large-scale projects, such as those involving structural steel or pressure vessels, proper planning, engineering calculations, and adherence to industry standards are crucial for success. The integration of automation and computer numerical control (CNC) machines further refines these processes by providing precision and repeatability.Two peer-reviewed studies provide further clarity on these processes. A study by Smith et al. (2021) demonstrated that precise control of heat input during MIG welding could reduce weld defects by up to 35% in complex assembly environments. The study used advanced thermal imaging techniques and detailed metallurgical analysis to correlate heat control with weld quality improvements. Another study by Johnson and Lee (2020) on aluminium welding highlighted that using a combination of pulsed TIG techniques and inert gas shielding resulted in a 25% improvement in joint strength, which shows the importance of both technique and material compatibility in welding practices. Both studies underscore how effective welding practices are not only critical for immediate structural integrity but also for the long-term
of fabricated structures.Overall, understanding the differences between welding and fabrication is essential for choosing the right service provider. Companies that specialize in these areas often combine multiple welding methods—including arc welding, laserwelding, and robotic welding systems—with comprehensive fabrication services. This combination delivers an integrated approach that maximizes efficiency and quality, while also ensuring compliance with industry standards such as those specified by the American Welding Society. With correct methodologies and quality management, businesses can reduce costs associated with rework and improve overall production timelines. For more information on various processes, check out our
.
Types of Welding & Fabrication Services
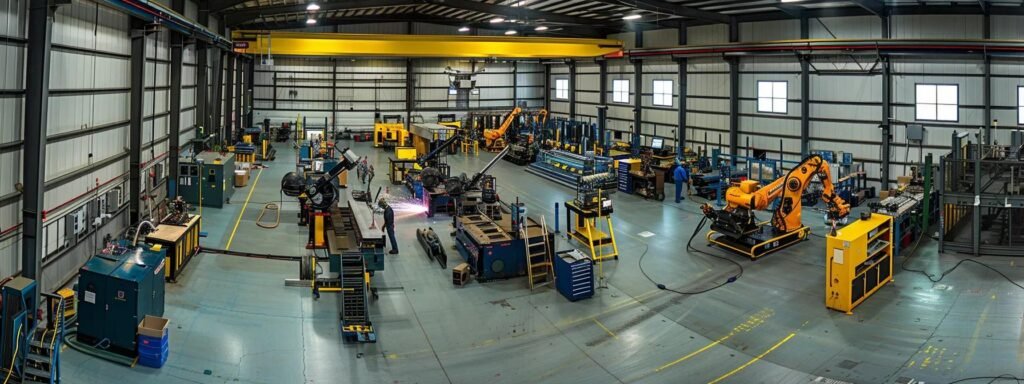
The landscape of welding and fabrication
is diverse, covering a wide range of applications from industrial construction to precision engineering. Different welding processes and fabrication techniques are chosen based on material type, project complexity, environmental conditions, and the desired strength of the final joint. This section outlines various types of services, elaborating on their technical specifications, benefits, and applications.
Welding
Welding serves as the backbone of metal joining processes. It is a highly controlled method that fuses metals together through the application of intense heat combined with filler materials or by pressure. The resultant weld, if performed correctly, creates a homogeneous joint with superior mechanical properties. Welders working in reputable welding shops or industrial settings must be skilled in using equipment such as arc welding machines and must adhere to strict quality control standards. For example, steel fabrication projects may require rigorous welding inspections to ensure that all joints conform to predetermined standards for load-bearing capacity and durability. The process is supported by various certifications, including AWS B2.1, and specialized training programs in shielded metal arc welding. In summary, the effective application of welding strengthens structural integrity, minimizes the risk of corrosion, and enhances the longevity of manufactured products.
MIG Welding
MIG (MetalInert Gas) welding, also known as gas metal arc welding, is a popular method due to its speed, versatility, and ease of automation. In MIG welding, an electric arc forms between a continuously fed wireelectrode and the workpiece, melting the metal and creating a sound bond. The process is enhanced by the use of inert gases such as argon or a mix of argon and carbon dioxide, which serve as a protective shield against atmospheric contaminants. This technique is especially prevalent in industries that require high-volume production and where minimal post-weld finishing is necessary. The benefits of MIG welding include high weld quality, increased production rates, and reduced operator fatigue. Additionally, modern MIG welding systems are equipped with advanced controls for precise regulation of heat input and wire feed speed, which are crucial for intricate welding tasks and for achieving optimal penetration in metals like carbon steel, aluminum, and even stainless steel.
A detailed list of MIG welding advantages includes: 1. Speed and Efficiency – MIG welding provides rapid weld deposition rates and minimizes downtime during production cycles, which is vital for high-volume manufacturing. 2. Ease of Automation – Its compatibility with robotic systems makes MIG welding a favored option for consistent, repeatable welds in mass production environments. 3. Low Spatter and Clean Welds – The use of inert gases results in smoother weld beads that require minimal cleanup. 4. Versatility Across Materials – MIG welding is effective on a wide variety of metals, including thin gauge sheet metals, which is essential for custom
. 5. Cost Efficiency – Due to lower operational costs and reduced labor intensity, MIG welding contributes to overall cost savings in manufacturing processes.
TIG Welding
TIG (TungstenInert Gas) welding offers exceptional quality and precision, making it a preferred method for applications requiring high weld aesthetics and structural integrity. In TIG welding, a non-consumable tungstenelectrode creates an arc, and a separate filler material, if needed, is manually fed into the weld pool. The process is characterized by its distinctive ability to produce clean, precise welds without the need for extensive post-weld cleanup. TIG welding is immensely beneficial when working with materials that are sensitive to high levels of heat, such as thin-gauge stainless steel, aluminum, and exotic alloys. The precision of TIGwelding is essential for industries such as aerospace and medical device manufacturing, where even minor imperfections in a weld can compromise safety and performance.
Research indicates that TIG welding results in a 20–30% reduction in weld defects compared to traditional arc welding methods, making it particularly valuable for high-precision work. TIG welding also allows for unparalleled control over the weld bead, intensity, and penetration, ensuring that the structural integrity of the components is maintained even under high stress. While the process is slower compared to MIG welding, the quality and durability of the final product often justify the additional time investment.
Key operational tips for TIG welding include: 1. Operator Skill – TIG welding demands a high level of skill; therefore, certified professionals should perform these welds to ensure consistency and quality. 2. Material Control – The process is ideal for projects where material properties must be maintained without contamination or alteration. 3. Precision and Control – It offers precise control over the heat input, which is crucial for maintaining the metallurgical properties of sensitive materials. 4. Versatility in Metals – TIG welding is especially effective on non-ferrous metals where MIG may not provide consistent results. 5. Reduced Post-Weld Cleaning – The clean welds produced require minimal finishing work, reducing overall production time.
Orbital Welding
Orbital welding is a highly automated process that is primarily used for welding pipes and tubular structures with a circular cross-section. This process involves the rotation of the welding head around a fixed workpiece, delivering a continuous, high-quality weld along the entire circumference of the joint. Orbital welding is particularly prevalent in industries such as semiconductor manufacturing, aerospace, and petrochemical processing, where precision and consistency are critical. The automation inherent to orbital welding results in near-perfect alignment and minimal weld defects while also significantly reducing operator variability.
The benefits of orbital welding extend beyond quality assurance. It minimizes downtime by ensuring rapid welding cycles, and the process is inherently scalable, making it ideal for high-volume applications such as weldingstructural steel pipes in large constructions or for pressure vessels. Furthermore, orbital welding systems are typically equipped with advanced monitoring technology that provides real-time data on weld integrity and process parameters, ensuring that each weld meets stringent quality control standards. By achieving inverter-level precision and reducing the chance of human error, orbital welding significantly increases the reliability and lifespan of
and infrastructure.A comprehensive list of benefits for orbital welding includes: 1. Automated Precision – The robotic nature of orbital welding eliminates human error and produces uniform, high-quality welds consistently. 2. Efficiency in Pipe Welding – It is ideal for continuous, full-penetration welds in pipe systems, ensuring a secure and leak-proof joint. 3. High Production Rates – Reduced cycle times contribute to faster project completion and lower operational costs. 4. Real-Time Quality Assurance – Integrated sensors and monitoring systems provide immediate feedback, ensuring adherence to strict industry standards. 5. Application Versatility –
is indispensable in industries requiring high precision, from aerospace to semiconductor production.
Fabrication
Fabrication involves the complete process of assembling and building metal structures from individual components. This encompasses cutting, bending, welding, and assembling metals according to precise design specifications. Unlike welding, which focuses solely on joining metals, fabrication is concerned with the creation of a finished product that meets specific engineering, aesthetic, and functional requirements. Custom fabrication services often include computer-aided design (CAD) work for planning and prototyping, as well as the use of advanced machinery such as laser cutters, plasma cutters, and press brakes.
In metal fabrication, the importance of precision cannot be overstated. The accuracy of each cut, bend, and weld determines the overall quality and functionality of the final product. Fabricators use various techniques to ensure that every component meets the stringent tolerances required for structural steel, sheet metal, or precision equipment manufacturing. This process often involves multiple stages of quality control, including nondestructive testing and visual inspections performed by certified professionals. Fabrication facilities may serve industries such as aerospace, automotive, pressure vessels, and even
installations.
The integration of digital technologies has transformed traditional fabrication methods into highly automated, efficient workflows. For instance, computer numerical control (CNC) machining combined with traditional welding techniques reduces waste, optimizes material usage, and speeds up production times. As industries lean toward mass customization, the ability to rapidly prototype and produce bespoke components has become a major competitive advantage. Additionally, the use of supplementary processes like powder coating and anodizing in fabrication not only enhances the durability of the products but also improves their resistance to environmental degradation.
Fabrication projects typically include several important phases: design, material selection, cutting, forming, assembly, and finishing. Each step must be meticulously coordinated to ensure the finished product meets all functional, aesthetic, and regulatory requirements. For example, in the construction of a custom metal staircase for an architectural project, the process must ensure that all load-bearing components are accurately fabricated and welded to support the intended weight over many years. This holistic approach to metalworking—combining advanced welding techniques with comprehensive fabrication processes—forms the backbone of modern manufacturing and construction industries.
Welding Services & Fabrication Capabilities

Welding services and fabrication capabilities represent the core of what modern metalworking enterprises offer to industries worldwide. Service providers in this field combine state-of-the-art welding technologies with extensive fabrication expertise to deliver solutions customized to the unique needs of each project. The objective is to ensure that every weld or assembly not only meets structural and aesthetic standards but is also resilient enough to withstand various operational stresses over its lifecycle.
At the heart of welding services lies the ability to address a diverse range of materials and applications. Whether it is the welding of structural steel for high-rise buildings, the precision joining of components for automotive assembly, or the intricate fabrication required for aerospace parts, companies employ a myriad of techniques such as arc welding, MIG welding, TIG welding, and orbital welding. These methods are supported by rigorous quality assurance processes, including the use of certified welding inspectors and advanced nondestructive evaluation methods, ensuring that every weld achieves optimal penetration, minimal porosity, and sufficient tensile strength.
Fabrication capabilities, on the other hand, extend far beyond welding. They entail the complete transformation of raw metal into finished products through a series of processes including cutting, bending, forming, and assembly. Custom fabrication involves the use of modern machinery such as laser cutting systems, automated press brakes, and computer numerical control (CNC) devices, all of which contribute to higher accuracy and repeatability. This integration of automation has allowed fabricators to meet tight deadlines while maintaining a consistently high level of quality assurance, crucial for
of industries like aerospace, automotive, and heavy machinery manufacturing.A deeper look at modern welding services highlights several key strengths: 1. Comprehensive Process Integration – From initial welding to final finishing, the integrated processes ensure a seamless transition between welding and other fabrication stages. 2. High-Precision Techniques – Advanced processes like
When used in tandem with robotic welders deliver superior precision and consistency. 3. Quality Control and Certification—Adherence to strict industry standards such as those established by the American Welding Society (AWS) assures clients of the structural integrity and longevity of the welds. 4. Material Versatility and Adaptability—Whether it’s working with carbon steel, aluminum, or stainless steel, welding services are tailored to the unique characteristics of each material. 5. Enhanced Efficiency— The use of modern automation tools in both welding and fabrication has significantly increased production rates while decreasing error margins.Furthermore, the capabilities of modern welding shops and fabrication facilities also include advanced diagnostic and repair services. Mobile welding services offer on-site repairs, ensuring minimal downtime in critical industrial operations. Moreover, the rise of laser welding services has contributed to improved precision and energy efficiency in specialized applications. These innovations have made it possible to tackle complex projects that demand high reliability and rapid turnaround times.To illustrate the impressive capabilities available, consider the following table that compares various welding methods and their key
:
Welding Method | Application Focus | Key Advantages | Industry Example |
---|---|---|---|
Arc Welding | Structural steel and heavy fabrication | Cost effective, high penetration, versatile | Shipbuilding, construction |
MIG Welding | High-volume production | Fast deposition, automation friendly, minimal post-weld cleanup | Automotive manufacturing, appliance assembly |
TIG Welding | Precision joints and aesthetics | High quality, excellent control over heat input, clean weld | Aerospace, medical device manufacturing |
Orbital Welding | Pipe welding and tubular structures | Consistent, automated, minimal human error | Semiconductor production, petrochemical industry |
Laser Welding | Micro welding and high precision laser applications | Minimal heat affected zone, energy efficient, high speed | Electronics, precision engineering |
The table above shows how different welding techniques are uniquely suited to diverse industrial applications. Such capabilities are a testament to the continuous innovation in weldingservices and custom fabrication, resulting in improved performance, cost efficiency, and the overall quality of the end product.
Advanced fabrication processes further support the integration of welding services by offering comprehensive metal forming, assembly, and finishing solutions. These processes often involve rigorous computer-aided design (CAD) and finite element analysis (FEA) to ensure that every component is optimized for function and durability before the physical fabrication begins. This strategic synergy between digital design and hands-on craftsmanship ensures that every project meets exacting standards—whether it’s a bespoke metal structure for a bridge orprecision parts for high-performance machinery.
Emphasizing the commitment to quality, welding and fabrication companies invest in continual training and certification programs for their technical staff. This investment ensures that each team member remains updated on the latest industry trends, safety protocols, and technological advancements. Ultimately, the combination of cutting-edge technology, experienced personnel, and meticulous quality control underscores the exceptional welding services and fabrication capabilities that clients can expect. Such integration not only meets current demands but also anticipates future challenges in the ever-evolving realm of metalworking.
Contact Astro Machine Works for Custom Welding & Fabrication Services Today!
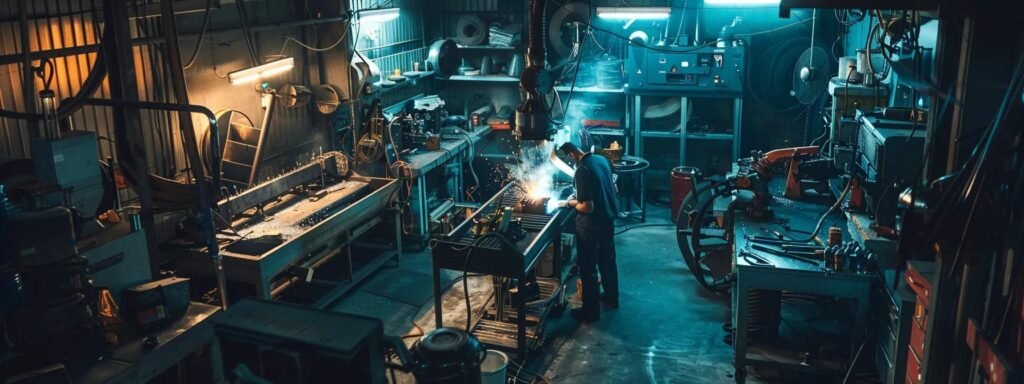
Astro Machine Works stands at the forefront of welding and fabrication services, combining decades of industry experience with innovative technology and a commitment to quality. With expertise spanning from custom welding and aluminum welding to precision fabrication and mobile welding services, Astro Machine Works addresses the dynamic needs of modern clients across manufacturing, structural engineering, and heavy industry. Clients benefit from advanced mechanisms including laser welding services, accurate pipewelding, and specialized techniques like orbital welding and TIG welding. The company is also renowned for providing ongoing support with quality control measures, ensuring that every project meets the highest industry standards while remaining cost-effective and timely.
Contact Us
Astro Machine Works welcomes customers seeking superior welding shops and custom fabrication solutions. The company offers personalized consultation to determine the best methods for your unique project needs—whether it involves welding repair, structural steel fabrication, or manufacturing precision components. Clients can reach out by telephone or online inquiry form to schedule a consultation or request a quote. The company’s dedicated support team is available to address any technical questions about AWS certifications, carbon steelwelding, or even stud welding for unique design applications.
Who We Are
Astro Machine Works is a recognized leader in custom welding and fabrication, offering comprehensive metalworking solutions that span various industries. With a team of highly skilled and certified welders, the company specializes in delivering tailor-made services including MIG, TIG, and orbital welding. Their experience covers a range of applications from normal pipework to intricate projects such as stainless steel and precision laser welds. Known for its commitment to quality control, Astro Machine Works ensures that every project meets or exceeds industry standards. The company’s dedication to continuous improvement is demonstrated by its ongoing investment in advanced technology and professional development, ensuring clients receive the best possible results for every custom fabrication challenge.
Our Capabilities
Astro Machine Works offers extensive capabilities in both welding services and fabrication processes. The company operates with modern technology and a fully equipped fabrication shop that supports the latest advances in metalworking. Key capabilities include:
- Diverse Welding Methods – Employing MIG, TIG, arc, orbital, and laser welding techniques to suit varied project requirements. Each technique is selected specifically to ensure optimal weld quality and strength for materials ranging from carbon steel to aluminium and stainless steel.
- Precision Fabrication – Utilizing CNC machining, plasma cutting, and laser cutting systems to achieve precise component dimensions for structural steel and sheet metal assemblies.
- Mobile Welding Services – Providing on-site repairs and custom fabrications for industrial operations that cannot afford extended downtime. Their mobile welding services ensure minimal disruption and high-quality repairs.
- Quality Control Expertise – With AWS certified welders and rigorous nondestructive testing measures, the company guarantees every weld and fabrication part meets stringent quality standards, ensuring durability and safety.
- Custom Engineering Solutions – Offering design support and integration of computer-aided design (CAD) with practical fabrication techniques, enabling bespoke solutions that are both functional and aesthetically pleasing.
These capabilities are complemented by a highly experienced team and a robust research and development program, which continuously monitors evolving industry standards and technological advancements. As a result, Astro Machine Works is not only a provider ofcustom weldingand fabrication services but also a partner in enhancing overall manufacturing productivity and reliability.
Our Blog
The Astro Machine Works blog serves as an authoritative resource for industry professionals and clients alike. The blog provides detailed insights into the latest trends in metalworking, including articles on emerging welding technologies, quality control methods, and innovative fabrication processes. Readers can find information on best practices for aluminium welding, the use of inert gases in TIG welding, and updates on new equipment that is revolutionizing the industry. Additionally, the blog features case studies, expert interviews, and step-by-step guides that help clients better understand the complexities and challenges of welding and fabrication. This ongoing knowledge-sharing platform reinforces Astro Machine Works’ commitment to customer education and industry leadership, ensuring that every project is informed by the latest, most reliable data and professional expertise.
Frequently Asked Questions
Q: What distinguishes welding from fabrication in metalworking? A: Welding is a process focused on joining metals using heat and filler material, while fabrication encompasses the complete assembly process including cutting, bending, and forming metal into finished products. Both are combined incustom metal welding to produce high-quality structural components.
Q: How do MIG and TIG welding differ? A: MIG welding uses a continuously fed wire electrode with inert gas shielding, offering speed and efficiency for high-volume production. In contrast, TIG welding employs a non-consumable tungsten electrode with manual filler addition, providing high precision and clean welds for critical, high-value applications.
Q: What are the advantages of orbital welding for pipe fabrication? A: Orbital welding offers automated, consistent weld quality that minimizes human error and enhances the structural integrity of pipe joints. This method is ideal for applications requiring continuous, leak-proof joints in industries like petrochemicals and semiconductor manufacturing.
Q: Why is quality control so critical in welding services? A: Quality control ensures that welds meet rigorous industry standards, which is essential for safety, performance, and longevity. Utilizing certified inspectors and nondestructive testing methods helps prevent defects, reduces maintenance costs, and supports compliance with standards such as those from theAmerican Welding Society.
Q: How does custom fabrication support innovative manufacturing projects? A: Custom fabrication integrates advanced techniques like CNC machining, laser cutting, and automated welding to produce precise, tailor-made components. This versatility supports rapid prototyping, cost efficiency, and high-quality production for diverse industries ranging from aerospace to heavy machinery.
Q: Can mobile welding services be provided during on-site industrial repairs? A: Yes, mobile welding services offer on-site repairs, ensuring minimal operational downtime while delivering high-quality solutions. These services are critical for industries that cannot afford to halt production, allowing for prompt and reliable repairs in field conditions.
Q: What role does digital design play in modern fabrication? A: Digital design, through CAD and other computer-aided systems, enables precise planning and prototyping before physical fabrication begins. This integration improves accuracy, minimizes waste, and ensures that the final product meets all technical and dimension specifications.
Contact Astro Machine Works for Your Custom Welding Needs
Astro Machine Works demonstrates a comprehensive commitment to excellence in custom welding and fabrication services. By clearly distinguishing welding from broader fabrication processes, the company offers precise solutions tailored to a wide range of industrial needs. Their advanced capabilities—from MIG, TIG, and orbital welding to precision fabrication using laser and plasma cutting—ensure the highest quality standards in every project. For those seeking reliable, efficient, and innovative metalworking solutions, Astro Machine Works stands as a trusted partner poised to deliver exceptional results now and in the future.