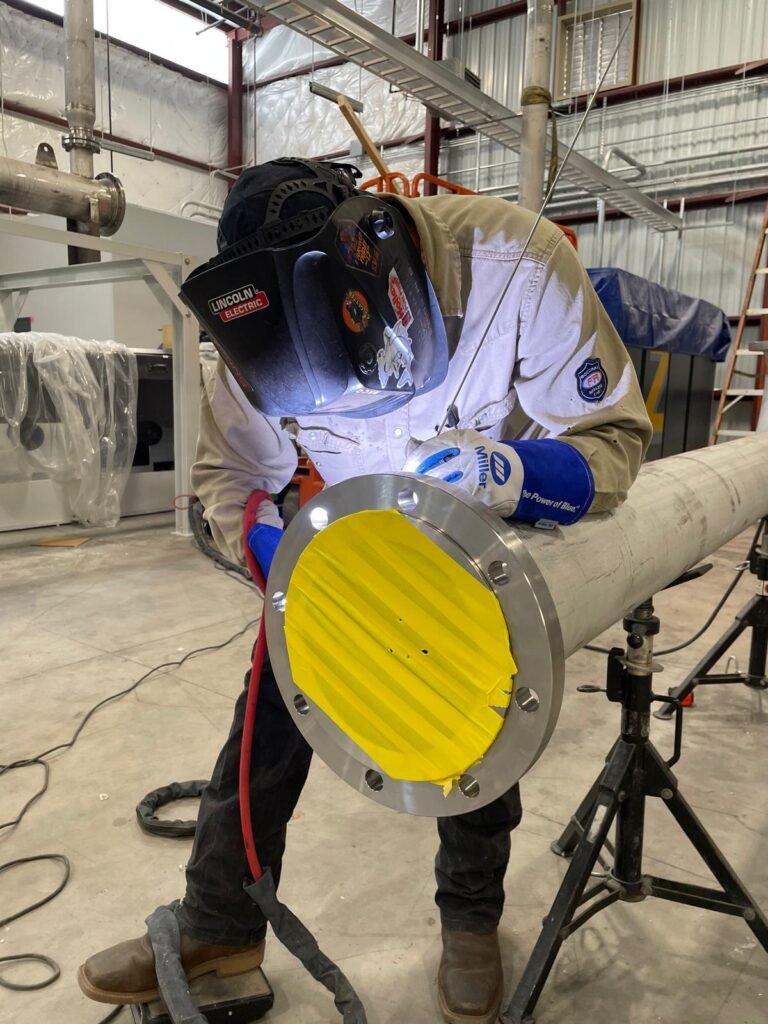
Stainless Steel Pipe Welding with Gas Purging Inside
Welding stainless steel pipes is a critical process in industries like food processing, pharmaceuticals, petrochemicals, and power generation, where corrosion resistance and weld quality are non-negotiable. One key technique to ensure high-quality welds is gas purging inside the pipe, a method that protects the weld root from oxidation and ensures structural integrity. Let’s explore why this is essential, how it’s done, and best practices for success. For more in-depth information, consider visiting stainless steel piping.
Why Gas Purging Matters
Gas purging is a crucial process that often goes unnoticed, yet it plays a significant role in various industrial applications, particularly in sectors like oil and gas, petrochemicals, and even food processing. As a professional in this field, I can attest to the importance of ensuring that systems are free from unwanted gases before initiating operations. The primary purpose of gas purgingis to remove air or other contaminants from a vessel or system to prevent potentially hazardous reactions, maintain product integrity, and enhance the overall efficiency of processes. By replacing these unwanted gases with an inert gas, we create an environment that mitigates risks, ensuring both safety and reliability.
Moreover,gas purging is not just essential for safety; it also affects the quality of the final product. In many cases, exposure to atmospheric gases can lead to oxidation, contamination, and spoilage, compromising the quality and efficacy of the materials involved. As someone who has worked with numerous processes where gas purity is critical, I’ve seen firsthand how effective purging can lead to improved outcomes, from consistency in product quality to higher yields. Additionally, it allows us to adhere to regulatory requirements, minimizing the likelihood of costly downtimes caused by contamination issues. Ultimately, gas purging is an indispensable practice that safeguards both operational integrity and product quality, reinforcing why it should never be overlooked in any industrial setting.
Stainless steel contains chromium, which gives it corrosion resistance by forming a protective oxide layer. However, during welding, exposure to oxygen at high temperatures can cause the chromium to oxidize on the inside of the pipe, leading to a rough, blackened appearance known as “sugaring” or “granulation.” This not only looks bad but weakens the weld, reduces flow efficiency, and creates sites for bacteria or corrosion—unacceptable in sanitary or high-purity applications. Gas purging displaces oxygen with an inert gas, typically argon, to prevent this reaction, resulting in a smooth, shiny, silver-colored weld root.
The Purging Process
Preparation: Before welding, clean the pipe’s interior and exterior to remove contaminants like oil, dirt, or rust. Proper fit-up is crucial—ensure the joint is aligned with a small gap (e.g., 1/16 to 1/8 inch) to allow gas flow andweld penetration.
Sealing the Pipe: Use purge dams, inflatable bladders, or plugs on both sides of the weld joint to contain the purge gas. Common materials include water-soluble paper, rubber stoppers, or specialized inflatable systems. Always include a vent hole on the opposite end to release displaced air and excess gas.
Gas Introduction: Connect an argon supply (the most common choice due to its inertness and availability) to one end of the pipe. Use a diffuser or gas lens to distribute the gas evenly and avoid turbulence, which can trap oxygen. Argon, heavier than air, should enter slowly from the bottom to push oxygen out through the vent.
Purging Time: Flow the gas long enough to displace the pipe’s internal volume several times—typically 7-10 times for stainless steel, reducing oxygen levels below 50-70 parts per million (ppm). An oxygen sensor or weld purge monitor can confirm when it’s safe to start welding.
Welding: Begin TIG(GTAW) welding, the preferred method for stainless steel pipes, while maintaining a low purge flow to avoid pressure buildup or “suckback” (concave weld roots). After the root pass, the purge can often be reduced or stopped, depending on the application thickness and code requirements.
Best Practices
Gas Choice: Argon is ideal for most stainless steels, but helium or argon-helium mixes can be used for thicker pipes or higher heat needs. Nitrogen is sometimes used for specific alloys (e.g., duplex stainlesssteel) but isn’t universally suitable due to potential nitride formation.
Flow Rate:
Start with a higher flow (e.g., 10-20 cubic feet per hour) to purge, then reduce to 2-5 CFH during welding to maintain stability without wasting gas.
Ventilation: Ensure the workspace is ventilated, as argon is an asphyxiant. Never enter a purged confined space without proper safety gear and training.
Monitoring:
For critical welds, use a purge monitor to verify oxygen levels. A shiny, silver root pass is the visual sign of success.
Benefits and Challenges
Gas purging ensures welds meet stringent codes (e.g., ASME B31.3 for process piping) and sanitary standards (e.g., AWS D18.1 for food-grade applications). It saves time and money in the long run by avoiding rework or product contamination. However, it requires setup time, additional equipment, and argon costs, which can add up on large projects. Innovations like Miller’s RMD® process (a modified short-circuit MIG) offer alternatives to eliminate purging in some cases, but TIG with purging remains the gold standard for precision and quality.
Conclusion
Welding stainless steel pipes with internal gas purging is a proven technique to achieve strong, clean, and corrosion-resistant welds. By mastering the process—preparation, sealing, gas flow, and monitoring—welders can deliver results that satisfy inspectors, clients, and end-users alike. Whether you’re piping chocolate milk or nuclear coolant, a good purge makes all the difference. For more on this technique, explore ourstainless steel piping services.